- Home
- Sustainability
- Society
- Customer Responsibility
- Customer Responsibility, Security, and Stable Energy Supply
Customer Responsibility, Security, and Stable Energy Supply
● Policies and Concepts
・ Customer Responsibility
The ITOCHU ENEX Group Customer Responsibility Policy
With a focus on energy, the ITOCHU ENEX Group engages in many different corporate activities in different regions. By putting the following into practice, we will seek for safety management and security to ensure, at any time, the safety of products and services supplied to customers, thereby fulfilling our responsibility for customers.
1.Controlling the qualitative safety of our products and recognizing the importance of security2.Observance of obligations specified in the laws relating to the safety of the products we handle
3.Promoting initiatives to ubiquitize safety control and security in the value chains
4.Encouraging in-house education regarding safety control and security
5.Establishing a route for the communication of information related to safety control and security
6.Prompt and appropriate actions in the event of an accident
・ Security
Basic Approach to Security
To stably supply energy to customers and enable them use to energy securely and safely, we are working to prevent accidents under the slogan,
Advertising and Marketing
Our View on Responsible Advertising and Marketing
Regarding its advertising and marketing activities, the ITOCHU ENEX Group puts into practice the following and engages in initiatives with sufficient consideration of our responsibilities to society, based on our Corporate Philosophy, “the best partner for life and society,” our Code of Conduct, “Be Ethical (Reliability and sincerity, creativity and ingenuity, transparency and integrity),” and Declaration of the Group Code of Conduct.
1. Advertising
• Creation and improvement of a brand guidebook designed to make our advertisements look visually cohesive, aiming to enhance our brand image and share it with customers
• Creation and improvement of in-house rules for placing ads with the right expressions and content on the right media outlets
• Sufficient consideration of defamation, discriminatory expressions, exaggerated and false expressions, religious faiths and political credos, the environment and the privacy, personal information and intellectual property rights of third parties
• Educational activities for the ITOCHU ENEX Group companies to encourage appropriate advertising
2. Marketing
• Compliance with related laws and in-house regulations and rules
• Thoroughly ensuring that our marketing activities do not infringe on others' rights, discredit or defame others, etc. and that the content and expressions used in our marketing will not be misunderstood
• Responsible marketing activities emphasizing dialogue with diverse stakeholders
● Structures and Systems
・ Safety Management Regime
Each division and group company selects a security manager. The security managers establishes basic approaches to security management, compliance with laws and regulations, thorough site management, understanding the security management status, preventing accidents, non-statutory security audits, etc. in a planned manner. Furthermore, each division and group company conducts security audits based on strict non-statutory security standards. They work to prevent accidents and the violation of laws by connecting facility management and security systems.
Car-Life Division | Group companies |
Industrial Business Division | Group companies |
Power & Utility Division | Group companies |
Home-Life Division | Group companies |
The role of chief security and safety officers |
・Formulation of basic safety management policies |
・Safety management instructions,commands, and education and preparation of independent safety standards |
・Monitoring of safety management |
・Accident prevention measures |
・Conduct of independent safety audits |
・Rigorous implementation of other environmental safety management activities |
・ LPWA(Low Power Wide Area)
The Group is working to increase the sophistication of security utilizing the LPWA LP gas centralized monitoring system. LPWA is a collective name for communication technologies featuring the ability to perform low-power wide-area wireless communications. Installing an LPWA device in a user's house enables 24-hour centralized monitoring, which enables automatic monitor reading, prevents accidents caused by people forgetting to extinguish fires, and predicts the timing for replacing gas containers in real time. ITOCHU ENEX HOME-LIFE CO., LTD. has been recognized for its proactive efforts to improve the security of LP gas by promoting the introduction of LPWA equipment, and has been certified as the "Gold Security Certified Operators), which is the highest level in the LP gas seller system.
・ Introduction of lorries equipped with contamination prevention devices.
To prevent contamination at gas stations, we have introduced lorries equipped with high-tech operation units. The introduction of this system has reduced human error and achieved safer unloading.
・ The digital transformation of security operations (introduction of tablets devices).
We have introduced tablet tools for inspections at LP gas facilities and gas stations. By using this system, we prevent people from forgetting inspections, provide appropriate expiration management for supplied device replacement, and prevent the expiration of devices due to management error. In addition, because it enables the real-time sharing of inspection results, we can respond to problems swiftly when they occur.
・ Acquisition of Quality Management (ISO 9001)
ITOCHU INDUSTRIAL GAS Co., Ltd., another company of the ITOCHU ENEX Group, acquired ISO 9001 (quality management system) international standard certification in 2000 concerning its work incidental to the manufacturing and sale of high-pressure gas, the reinspection of high-pressure gas containers and their accessories, the import and inspection of high-pressure gas containers and miscellaneous procedures involving high-pressure gas containers. Our group company, ITOCHU INDUSTRIAL GAS Co., Ltd. has obtained ISO 9001 certification. ISO 9001 is an international standard whose goal is the improvement of the quality of products and services. It has also obtained the VDA(2021) trademark certification together with the manufacturing of AdBlue® aqueous urea and U.S. Department of Transportation (DOT,2022) certification of gas containers for aircraft, and is working to maintain and improve quality management in each business.
● Initiatives Within the Group
・ Delivery of Security Information
ITOCHU ENEX Home-Life Group, which handles LP gas, etc., delivers security information to dealers when needed via a division magazine and D-NEXT, a LINE information delivery service.
The Home-Life Group, which handles gasoline and light oil, etc., distributes the Guidelines for CS, Car-Life Station, operation to each CS in order to ensure the safety of petroleum products and CS facilities. Via the Guidelines, they provide thorough security guidance including on the main operations of hazardous materials security superintendents, the regular inspection of facilities and equipment, fire and accident prevention training, and the proper treatment of industrial waste.
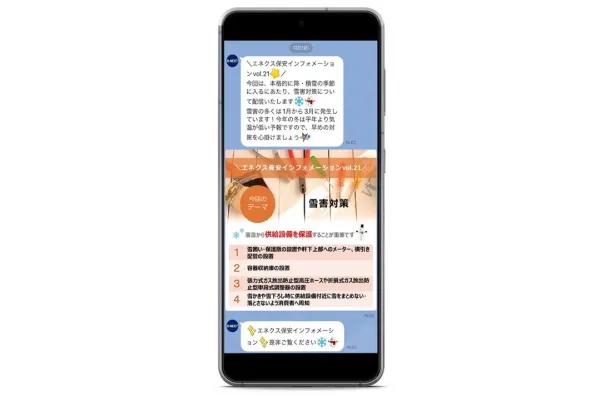
・ Assistance for Obtaining Qualifications
The Group provides in-house study meetings and e-learning programs. The Home-Life Division also provides a variety of training content internally for workers and for dealers using D-NEXT Challenge. In addition, at the first lecture for cultivating LPG Installation Engineers certified by the Ministry of Economy, Trade and Industry held at ITOCHU ENEX Technical Training Center, we established the first on-demand learning program in Japan to respond to the increasing diversity of learning environments.

・ Initiatives at The Etajima Terminal Base
The Etajima Terminal, which stores and manages petroleum and chemicals, is designated as a special disaster prevention area for petroleum complexes and is fully equipped with disaster prevention equipment such as fire trucks and fixed fire extinguishing equipment. The employees receive disaster prevention education and annual disaster drills every month to acquire knowledge and skills. In addition, all employees working at the Etajima Terminal live in areas where they can quickly come to the terminal. We have built a system that can respond immediately in case of a natural disaster.
・ Safety meetings at the asphalt plant (conducted monthly).
The Industrial Business Division, which has asphalt bases, holds safety meetings every month with security personnel and people involved in bases and transportation to inspect tanks and piping equipment and check that the rules for transportation, loading, unloading, etc. are observed aiming to ensure safety.
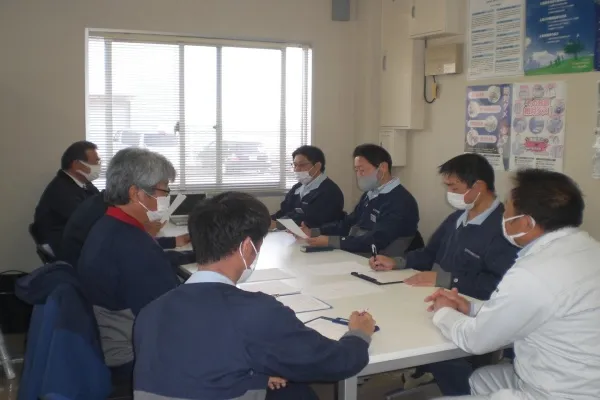
・ Promotion of Safe Driving
We strive to prevent vehicle accidents by appointing a safe driving manager based on our Vehicle Management Rules, aiming to promote vehicle management and safe driving, ensure the safety of our employees, and improve their awareness of safe driving. In addition, since FY2022, we have introduced safe driving lectures and practical training as a system for preventing accidents involving commercial vehicles and for people who have a driver's license but never drive when they are assigned to a division where commercial vehicles are used.
The Group is working on the improvement of health and safety in the workplace at all offices to prevent accidents. In FY2022 and FY2023, there was no material incidents.
● Collaboration with Outside Initiatives
For details, please refer to "Supply Chain"● Response to Natural Disasters and Disaster Prevention
The Group's foremost mission is to provide a stable supply of energy in line with its corporate philosophy.
As such, the Group provides infrastructure maintenance capabilities across Japan to ensure that the safe and reliable delivery of energy needed by customers is maintained as far as possible. In addition, the Group is promoting establishment of bases that can assist local governments and communities in strengthening regional disaster prevention efforts.
■ Our Infrastructure Network Sales bases (12 sites)
ITOCHU ENEX Group has sales bases all over Japan. When a disaster occurs, our network can connect the disaster region to the rest of Japan, enabling Group-wide support for disaster relief and recovery.
■ LP gas core filling stations (13 nationwide)
ITOCHU ENEX Group operates 13 core filling stations capable of maintaining stable supplies of LP gas even in times of disaster. Core filling stations are equipped with disaster infrastructure maintenance functions (private power generation facilities, automobile fuel filling facilities, satellite telephones, etc.), and protect the safety and security of local communities by enabling the stable supply of LP gas to affected areas even in the event of a disaster.
There are 14 offices nationwide equipped with disaster-response bulk systems that enable bulk power generation, hot water supply, and food preparation using LP gas, ensuring an energy lifeline for evacuation centers in times of disaster.
■ Disaster Response Stations (129 nationwide/CS)
In the CSs(*) of each area, These stations are equipped with emergency generators to maintain refueling functions, and can quickly supply electricity to maintain refueling functions even in a power outage caused by a disaster.
*CS is an abbreviation for Car-Life Station. It is a service station proposed by ITOCHU ENEX Group and provides multiple services.
■ Kizuna Net Center (1 site in Miyagi)
The Kizuna Net Center (operated by Enex Fleet Co., Ltd.) began operating in 2012 as part of reconstruction support following the Great East Japan Earthquake, and contributes to safe, secure community life. As an energy supply base during times of disaster, it offers a priority supply to evacuation centers and hospitals, and is capable of maintaining stable supplies even during a power outage with its fully self-sufficient energy supply equipment. It also issues guidance for the restoration operations of emergency restoration stations.
■ Emergency water for firefighting and domestic water (8 areas)
Of the district heat supply plants operated by Group company Tokyo Toshi Service Co., Ltd., the heat storage tanks in 8 areas can be used as local community tanks and supply water for fi refighting and domestic water(water for miscellaneous use other than drinking water) in emergencies. The heat storage tanks in the 8 areas have a total capacity of 61,550 m3.
*Reference: The water volume of 20,000m3 can supply about 60,000 people for about 10 days.
・ Disaster prevention agreements (With 7 local governments)
We have entered into agreements for community planning for disaster prevention, and for prioritizing supply to evacuation centers, hospitals and emergency vehicles.
・ Diverse human resources and systems to support living infrastructure
Our group has about 250 employees nationwide who are certified disaster prevention specialists. As a company that supports social infrastructure, we support society and people's lives by having a diverse workforce that can quickly respond to situations as a group, from pre-disaster preparation to post-disaster recovery.
We have also formulated a business continuity plan (BCP) in preparation for the occurrence of a large-scale disaster. The BCP/Disaster Response Headquarters, which is the core organization of this plan, is responsible for responding to disaster situations, developing appropriate coordination systems with the rest of the country, and conducting periodic reviews. In addition, a backup system has been established to ensure that the functions of the headquarters will not be lost in the event of major damage to Tokyo, such as in the case of an earthquake directly under the Tokyo metropolitan area (the system is transferred to the Fukuoka and Hiroshima areas).
・ Emergency Lifesaving and Disaster Response
Various Initiatives | ・Holding ordinary lifesaving training courses ・Displaying emergency first-aid manuals ・Providing lifesaving equipment, disaster readiness supplies/provisions and equipment, and disaster readiness (hazard and evacuation) maps ・Conducting disaster readiness and evacuation drills ・Supporting employees in obtaining disaster readiness qualifications (over 200 employees have already obtained qualifications) ・Conducting regular BCP (Business Continuity Planning) activities ・Establishing disaster-response vendors ・Satellite telephones carried by people in charge of disaster control at the head office and specific areas ・System for confirming the safety of employees ・Establishing an emergency contact network |
---|